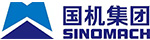
文章出處:知識中心 網(wǎng)責任編輯: 洛陽軸承 閱讀量: 發(fā)表時間:2021-09-10 08:31:55
大型滾動軸承整體結構尺寸大,普遍存在偏載、變載、潤滑不良等復雜工況,其力學特性、故障模式以及壽命等具有特殊性。作者從大型滾動軸承結構和工況特點出發(fā),評述了軸承結構力學分析、測試與監(jiān)測、故障模式、壽命與故障剩余壽命等方面的代表性研究成果,進而探討了大型滾動軸承這幾方面內(nèi)容后續(xù)研究的具體思路。
作者首先對大型滾動軸承的典型應用(風電機組、隧道掘進機刀盤、大軸重鐵路貨車)中的軸承結構特點進行了介紹,接著分析了大型滾動軸承的結構力學、測試與檢測技術的國內(nèi)外研究現(xiàn)狀。這里重點對大型軸承的故障和壽命的相關研究進行分享。
大型滾動軸承的大尺寸帶來了制造、安裝、運行維護的一系列問題:缺少系統(tǒng)化的設計制造技術,設計和制造精度不易保證,熱處理困難,潤滑質(zhì)量不易保障,安裝精度不易控制,密封困等;在重載、偏載、變載等復雜工況的作用下,局部承載強度會顯著增加且變化頻繁;軸承溫度場和潤滑流場的不均勻還會進一步惡化軸承工作狀態(tài),導致過早出現(xiàn)局部磨損、損傷乃至失效。
如圖6所示,滾動軸承壽命的定義可以劃分為3個階段:
1)疲勞壽命,指軸承在給定循環(huán)載荷條件下運行至發(fā)生疲勞剝落的時間,通常根據(jù)S-N曲線得到;
2)剩余疲勞壽命,指軸承在給定循環(huán)載荷條件下累積運行一段時間后繼續(xù)在該條件下運行到剝落的時間;
3)故障剩余壽命,指軸承在實際工況下累積運行一段時間發(fā)生故障后繼續(xù)運行至失效的時間。大型重載軸承的故障形式具有特殊性,很多情況下是由于故障導致壽命終止而不是常規(guī)的疲勞壽命問題,即故障剩余壽命指標更為重要。
圖6 軸承壽命示意圖
Fig.6 Diagram of bearing life
一、典型故障模式
目前,工程中常見的風電機組轉(zhuǎn)盤軸承失效模式主要有套圈斷裂、保持架斷裂、保持架磨損、密封圈漏脂等,如圖7所示。
圖7 風電機組轉(zhuǎn)盤軸承的典型故障形式
Fig.7 Typical fault mode of wind turbine slewing bearing
掘進機主軸承的故障主要有齒圈斷裂、密封失效等,如圖8所示。
圖8 掘進機主軸承的典型故障形式
Fig.8 Typical fault mode of main bearing for TBM
鐵路貨車軸承的故障形式主要有2類:1)由于軸承受擠壓以及摩擦載荷的周期性作用,滾道表層下方的組織出現(xiàn)疲勞并產(chǎn)生細微裂紋,隨著微裂紋的逐漸擴展最終產(chǎn)生由內(nèi)而外的剝落;2)由于密封不良和潤滑劣化導致的過熱故障(圖9),約占總故障的72%,這是導致鐵路貨車軸承實際使用壽命縮短的關鍵原因,故障加劇時甚至會引發(fā)切軸等重大事故。
圖9 鐵路貨車軸承過熱故障示意圖
Fig.9 Overheating fault diagram of railway freight bearing
此外,滾道和滾動體表面的軸向裂紋和次表面的白蝕裂紋( White Etching Crack , WEC)被認為是造成軸承過早失效的根本原因,風電齒輪箱軸承經(jīng)常會出現(xiàn)此類故障,該方面的研究得到了軸承行業(yè)、工程技術界和學術界等多領域研究人員的高度重視。無論表現(xiàn)方式如何,軸承的早期失效總是遵循短板原則:當潤滑不良或接觸面不光滑時,接觸表面為短板,軸承失效往往由表面磨損等引起;當潤滑良好時,次表面為短板,軸承失效則往往由次表面處的材料缺陷或應力集中所引起。大尺寸軸承容易發(fā)生大的局部變形,導致嚴重磨損以及局部應力集中,進而導致軸承故障,發(fā)生提前失效。
二、軸承壽命研究現(xiàn)狀
2.1 國外相關研究
國外對滾動軸承疲勞壽命的研究開始較早,特別是SKF,F(xiàn)AG和NSK等大型軸承企業(yè)及NASA等科研機構,已經(jīng)形成了一套比較完善的理論。目前,常用的滾動軸承疲勞壽命理論有L-P壽命理論,I-H壽命理論,Zaretsky壽命理論。
1947年至1952年,文獻[70]基于韋布爾理論提出了L-P壽命理論,通過生產(chǎn)實踐的不斷修正,最終被ANSI/ABMA/ISO等標準采納。1985年,文獻[71]在L-P壽命理論的基礎上,將極限疲勞剪切應力的概念引入滾動軸承疲勞壽命的研究中,提出了一種新的滾動軸承疲勞壽命理論,并于1990年通過對渦輪發(fā)動機主軸球軸承的研究最終確立了I-H壽命理論。文獻[73]通過對滾動軸承材料和滾動體疲勞壽命數(shù)據(jù)的大量研究,分開考慮應力-壽命系數(shù)和韋布爾系數(shù),重新建立軸承失效概率函數(shù)并提出了一種新的軸承疲勞壽命理論。在理論分析上,L-P壽命理論和I-H壽命理論都建立在韋布爾分布的基礎上,而Zaretsky則是重新建立了韋布爾分布函數(shù)。2012年,文獻[74]忽略軸承支承及套圈變形對滾動體上載荷分布的影響,將靜強度理論引入軸承疲勞壽命模型,獲得了大型轉(zhuǎn)盤軸承的疲勞壽命,與ISO結果的對比驗證了該模型的準確性。2016年,文獻[75]基于NREL設計指南中的風電機組變槳、偏航軸承標準,利用Romax軟件計算2.5 MW風電機組變槳、偏航軸承的壽命,結果表明使用NREL指南計算的壽命值比使用Romax軟件得出的值更保守。盡管NREL設計指南與Romax分析結果存在一些差異,但由于NREL設計指南具有簡單性和保守輸出特性的優(yōu)點,可將其用于變槳軸承和偏航軸承的初始設計。
從上述理論中可以看出,相互作用零件間的接觸應力-應變特性是影響軸承疲勞失效模式的主要原因。因此,學者們進行了基于彈性動力學理論的疲勞失效機理研究:文獻[76]基于彈流動力潤滑理論首先獲得了線接觸兩彈性體次表面三坐標方向上的主應力與切應力,接觸表面正壓力與摩擦力的力學關系;文獻[77]研究發(fā)現(xiàn)次表層最大剪應力隨著疲勞累積逐漸向表層移動,由于安裝損傷、表面夾雜物和潤滑污染導致的應力集中,使萌生于次表層最大應力處的裂紋加速向表面擴展,形成麻點、剝落等故障;文獻[78]基于彈性動力學理論進一步優(yōu)化設計了普通軸承的疲勞壽命;文獻[79]基于彈塑性理論建立了球與溝道接觸有限元模型,首次獲得了兩零件接觸區(qū)的應力分布;文獻[ 80]針對大型三排圓柱滾子軸承,考慮軸承的幾何參數(shù),計算了軸承動態(tài)承載時的內(nèi)部接觸應力分布,將滾道的接觸疲勞失效作為軸承壽命的判據(jù)。
在對軸承失效機理進行分析的基礎上,學者們通過考慮特定因素對軸承壽命的影響進一步完善軸承壽命模型;文獻[81]引入Archard磨損模型和Lemaitre損傷模型,并與加速壽命試驗相結合提出了利用少量材料表征試驗進行軸承壽命預測的可靠方法;文獻[82]研究了經(jīng)過精密硬車削、磨削加工的軸承套圈的表面完整性對疲勞壽命的影響;文獻[83]基于蠕變機理的表面損傷積分,將軸承局部摩擦引起的軸承異常生熱引入軸承壽命的計算;文獻[84]基于試驗分析得到的高承載和振蕩運動條件下的磨損信號和摩擦力矩的變化規(guī)律,提出了能夠表征軸承剩余壽命的退化模型;文獻[85]提出了一種同時考慮工況參數(shù)和工況監(jiān)測信號的韋布爾加速失效時間回歸(WAFTR)模型進行軸承壽命預測;文獻[86]提出以滾道表面生存概率為核心的滾動接觸基本壽命計算的新方法。
2.2 國內(nèi)相關研究
國內(nèi)的相關研究主要是考慮不同因素對大型滾動軸承的疲勞壽命模型進行修正:文獻[87]基于統(tǒng)計學理論分析了大型滾動軸承的疲勞壽命及其可靠性,結果表明大型滾動軸承疲勞壽命服從三參數(shù)的韋布爾分布,為其壽命及可靠性評價提供理論指導;文獻[88]考慮軸承潤滑和游隙變化,對軸承壽命計算理論進行了修正;文獻[89]引入了偏航、變槳軸承在軸向力、徑向力和傾覆力矩共同作用下的影響,計算了考慮偏航、變槳軸承內(nèi)、外圈疲勞壽命的軸承整體疲勞壽命;文獻[90]針對雙列四點接觸球軸承的受力特點,提出了考慮軸向載荷、徑向載荷和傾覆力矩的軸承應力分布計算方法,基于L-P壽命理論計算了當量動載荷和額定動載荷下的軸承壽命。
三、軸承狀態(tài)評價與剩余命預測研究現(xiàn)狀
軸承狀態(tài)評價與剩余壽命預測是進行軸承視情維修,及時發(fā)現(xiàn)問題,減少經(jīng)濟損失的主要途徑。
3.1 狀態(tài)評價
基于振動信號的軸承故障診斷與預測是判斷軸承退化狀態(tài)的常用方法:文獻[4]對軸承故障信號的本征模態(tài)函數(shù)進行快速傅里葉變換獲得了滿意的診斷效果;文獻[5]基于多域特征、改進的距離判別技術和改進模糊自適應共振理論映射(A-daptive Resonance Theory Map,ARTMAP)提出了一種新的兼具魯棒性和穩(wěn)定性的軸承故障智能診斷方法;文獻[6]利用主成分分析( Principle Compo-nent Analysis,PCA)和人工神經(jīng)網(wǎng)絡( Artificial Neural Network,ANN)分別結合重標極差法和去趨勢波動分析法對不同轉(zhuǎn)速和外載荷工況下的3種損傷程度軸承故障進行診斷,結果表明4種算法組合都能有效地進行故障監(jiān)測和診斷。
然而,上述成果中涉及的軸承故障均為人為預制故障,與軸承實際運行過程中出現(xiàn)的故障不符,無法對軸承運行狀態(tài)進行有效劃分。因此,需要對跑合過程中的軸承零件進行分析,以獲得真實的軸承運行狀態(tài)。文獻[91]在對工作次表面形貌直接分析的基礎上,將滾動軸承損傷退化過程分為跑合、平穩(wěn)和非穩(wěn)態(tài)3個階段;文獻[92-93]進一步將損傷退化過程劃分為跑合、平穩(wěn)、損傷發(fā)生、損傷演化、損傷發(fā)展5個階段,并對已有的研究和試驗工作進行了總結梳理,為故障與壽命的關系分析提出了新思路,還指出實際過程中的故障信號形式與仿真結果不同,需要針對不同的磨損演化過程建立特定的故障診斷、評估和預測方法。
3.2 剩余壽命預測
現(xiàn)有的軸承壽命預測分為基于物理模型和基于數(shù)據(jù)驅(qū)動的2類方法?;谖锢砟P偷姆椒ㄍㄟ^彈性斷裂力學和疲勞裂紋擴展理論進行軸承失效機理分析,建立軸承壽命模型,利用模型預測軸承有效剩余壽命,并通過修正模型參數(shù)提高預測精度。文獻[94-95]首先提出軸承疲勞裂紋擴展模型,文獻[96]將該模型從一維擴展到二維,文獻[97]通過分析指出傳統(tǒng)的裂紋擴展模型無法滿足帶有碎裂問題軸承的壽命計算,文獻[98]考慮非線性隨機問題提出了基于裂紋擴展的軸承剩余壽命預測方法。此外,文獻[99]提出了帶有碎裂萌生的軸承的接觸疲勞失效壽命預測方法。上述基于物理模型的軸承剩余壽命預測由基于材料疲勞破壞的壽命設計準則獲得,未考慮軸承故障產(chǎn)生及其退化,直至失效所引起的壽命損失,以及相應的故障剩余壽命。
基于人工智能與統(tǒng)計的軸承壽命預測方法屬于數(shù)據(jù)驅(qū)動方法。其中,人工智能方法通過智能算法的優(yōu)化組合,利用機器學習算法對獲得的數(shù)據(jù)進行擬合,獲得軸承全壽命過程的演化規(guī)律,通過設定合理閾值進行軸承壽命預測。文獻[100]提出了一種基于支持向量機(SupportVectorMa-chine ,SVM)的軸承剩余壽命預測方法,分別利用仿真和試驗數(shù)據(jù)訓練SVM,結果表明訓練獲得的SVM能夠預測軸承失效時間;文獻[101]將關聯(lián)向量機和邏輯回歸結合,提出了一種新的預測方法以評估故障劣化和剩余壽命,并利用單套軸承的仿真和試驗數(shù)據(jù)對預測效果進行驗證。神經(jīng)網(wǎng)絡是一種被廣泛應用于預測技術的智能算法:文獻[102-103]分別利用反向傳播神經(jīng)網(wǎng)絡(Back Propagation Neural Network,BPNN)進行了軸承剩余壽命預測;文獻[104]基于韋布爾分布和人工神經(jīng)網(wǎng)絡進行軸承故障預測與健康管理研究,提出了一種精確的軸承剩余壽命預測方法;文獻[105]基于振動信號,采用高斯隱馬爾科夫模型( Gaussi-ans Hidden Markov Model,GHMM )進行軸承特征提取以及剩余壽命的預測;文獻[106]通過時域特征參數(shù)對人工螞蟻聚類進行訓練獲得軸承性能退化狀態(tài),利用隱馬爾科夫模型( Hidden Markov Model,HMM)進行軸承壽命預測;文獻[107]基于時域、頻域和小波包分解特征,利用隱馬爾科夫模型進行軸承故障診斷和剩余有效壽命預測;文獻[108]基于隱半馬爾科夫模型( Hidden Semi-MarkovModel,HSMM)通過實時數(shù)據(jù)處理獲得軸承所處狀態(tài)以及狀態(tài)轉(zhuǎn)移的概率,完成軸承剩余壽命預測。
統(tǒng)計法基于軸承狀態(tài)和響應數(shù)據(jù)對軸承運行趨勢進行預測,獲得軸承剩余壽命分布曲線。然而,由于工作環(huán)境和測試技術的限制,軸承運行狀態(tài)無法直接測量,僅能通過與軸承運行狀態(tài)相關的響應參數(shù)(如振動信號、溫度)間接反映軸承性能退化過程。由于軸承狀態(tài)退化過程涉及到多個物理量,單一的測量、特征參數(shù)不能全面反映軸承退化狀態(tài),需要融合多個物理量進行軸承性能退化狀態(tài)的評價,并引入壽命模型進行剩余壽命預測。而且,對于大型滾動軸承其失效、破壞往往來自于故障,幾乎看不到因材料疲勞所引起的壽命終止,然而并未見到考慮故障進行大型滾動軸承剩余壽命預測的相關報道。因此,大型滾動軸承的壽命預測應該在多物理量測試的基礎上,結合故障診斷、故障失效模式和退化機制開展。
(參考文獻略)
來源:《軸承》2021年9期(節(jié)選)
作者:韓清凱,云向河,李寧,溫保崗,王平
第一作者簡介:韓清凱,東北大學機械工程與自動化學院,教授,《軸承》編委。長期從事重大機械裝備動力學設計與機電系統(tǒng)研發(fā)、軸承數(shù)字化設計與試驗、機械狀態(tài)監(jiān)測與診斷、振動噪聲控制等領域的科研工作。已出版著作10余部,發(fā)表論文200余篇,取得專利20余項。
引文格式:
韓清凱,云向河,李寧,等.大型滾動軸承故障診斷及壽命評估技術進展[J].軸承,2021(9):1-13.
軸研所公眾號 軸承雜志社公眾號
營銷熱線
0379-64367521
0379-64880626
13693806700
0379-64880057
0379-64881181